⚡ Wakeboarding Without the Noise: Engineering an All-Electric Wakeboat That Performs
- Tóth Ádám
- 7 days ago
- 3 min read
At Drivetrain Innovation, we thrive on challenges that push technology into new territory. So when we were approached to electrify a Malibu 24MXZ wakeboat for use on Austria’s Wörthersee lake, we knew we were in for something special.
The goal was ambitious: deliver a drivetrain that could match or outperform the power of an internal combustion engine, provide all-day operation, and meet the region’s strict electric-only licensing rules — all in a high-performance wakeboard taxi.
Making Power Work on Water
The heart of the system was the Emrax 348, a high-efficiency axial flux motor known for its power density. But to meet the demands of this application, we needed to push the Emrax to its full potential — something no existing controller on the market could handle on its own.
The motor’s dual-winding architecture gave us an opening: we connected two of our HV-500 controllers, (a former revision of our current HV-550 and HV-850 generation), each driving one of the windings. That move came with its own challenge — coordinating two independent controllers to act as one.
This is where we stepped in with something new.
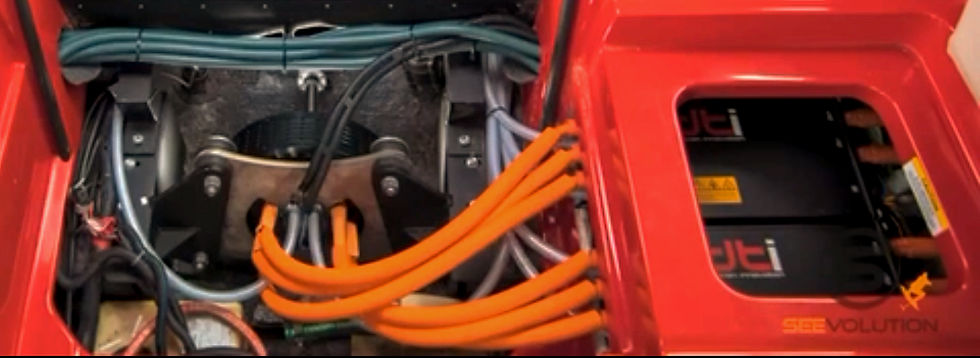
We engineered a custom encoder splitter, allowing both inverters to read the same position sensor while staying perfectly in sync. This wasn't just a patch — it was the seed for a new system architecture.
From there, we implemented our first-ever stacked controller setup, using a primary-secondary control configuration. That architecture has since evolved dramatically. Today, with our refined encoder splitter and scalable software, we can theoretically support up to 253 synchronized controllers — a breakthrough for multi-inverter applications in marine, aviation, and heavy-duty EVs.
Building the Full System
Beyond motor control, the project included a full high-voltage system design. We integrated:
Two Tesla Model S battery packs, providing 800V DC
A custom-built PDU and precharge controller
Our Drivetrain Innovation BMS (currently in development)
A Stercom 22kW onboard charger for rapid turnaround at the dock
Thermal performance became one of the most critical areas to get right. Under sustained load, the initial cooling setup showed its limits — pushing us to redesign the cooling loop entirely. That work directly fed into the development of our next-generation HV-550 controller, which now features superior thermal handling and a longer sustained power profile.
We also re-evaluated the customer-selected pumps and heat exchangers, helping tune the system for real-world marine conditions where continuous, high-load performance is essential.
With the on-board system successfully integrated, we can safely say this is boat makes a full-fledged fun machine on water.
The Result: Silent Power That Pulls Hard
Once on the water, the boat spoke for itself — or more accurately, didn’t.
With well over 300kW of peak power, the boat easily reached speeds above 70 kilometers per hour, and the torque delivery was immediate and smooth. No fumes. No engine noise. Just clean, instant power that left nothing but a wake behind.
And with the Tesla battery packs supplying deep capacity, the boat had enough range to operate all day without compromise — exactly as intended.

Looking Ahead
This project didn’t just achieve its goal — it pushed our technology forward. It was the starting point for our now-scalable, multi-controller drivetrain architecture. And with our growing collaboration alongside LXNAV Marine, we believe electric power has a bright future in the marine world.
The performance is here. The technology is here. And the ride is better than ever.